Industrial Powder Coating Equipment: Advanced Pretreatment Solutions
Pretreatment forms the essential foundation of all durable powder-coated finishes. This vital stage in industrial powder coating equipment rigorously removes oils, rust, and contaminants while chemically preparing metal surfaces for optimal powder adhesion. Two proven methods dominate modern systems: spray pretreatment propels high-pressure solutions through conveyorized tunnels for rapid cleaning, while dip-tank pretreatment submerges parts in sequenced chemical baths for complete coverage.
Neglecting this step risks costly failures – improper pretreatment contributes to 80% of coating defects, from peeling to corrosion. This guide demystifies both approaches to align your coating challenges with the ideal solution.
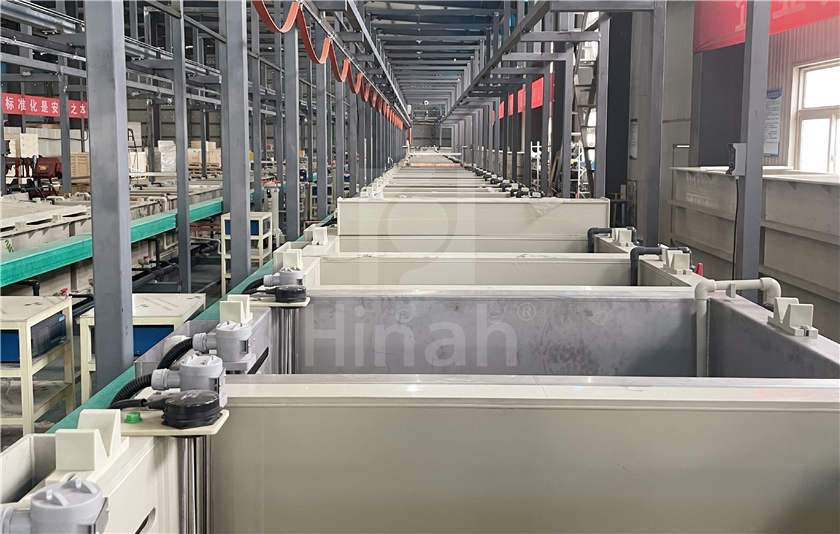
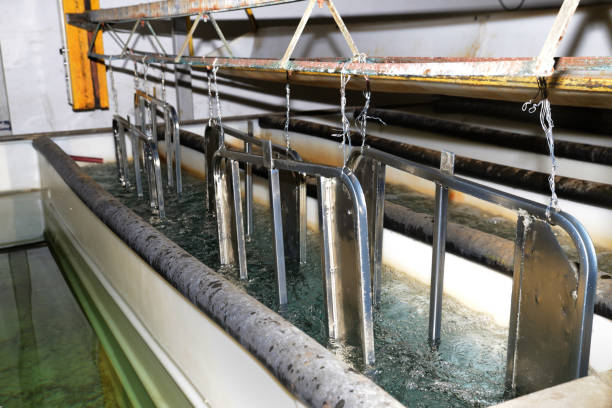
I. What is Pretreatment in Powder Coating?
Pretreatment is the mandatory cleaning and chemical preparation stage before powder application. In industrial powder coating equipment, this process:
- Removes contaminants (oils, rust, dirt)
- Creates a conversion layer (e.g., zinc phosphate) for adhesion
- Rinses residues to prevent contamination
Two core methods deliver this:
- Spray Pretreatment
High-pressure chemical jets clean surfaces in automated tunnels – ideal for flat/simple parts.
- Dip-tank Pretreatment
Parts submerged in sequential chemical baths – ensures 360° coverage for complex geometries.
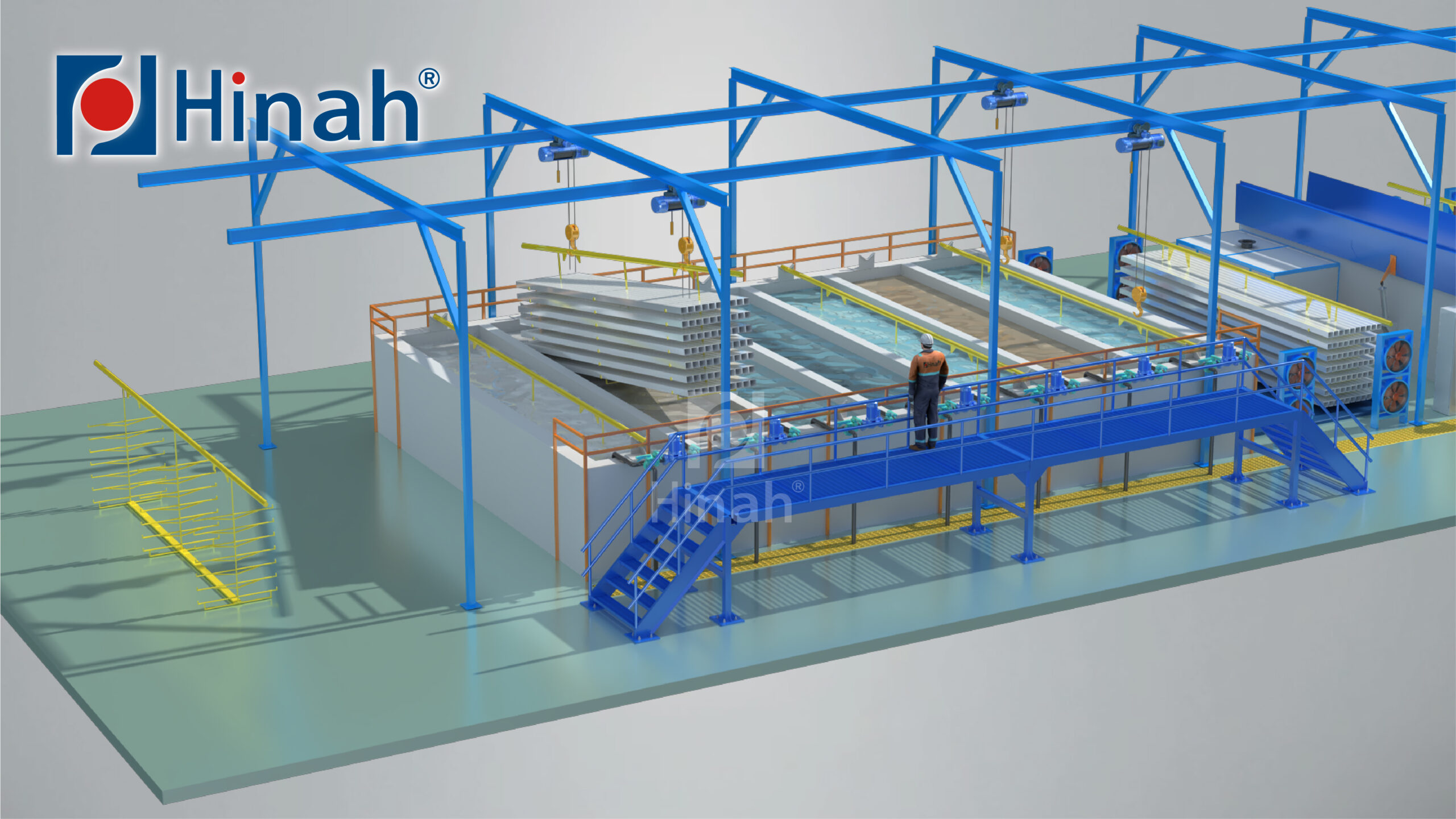
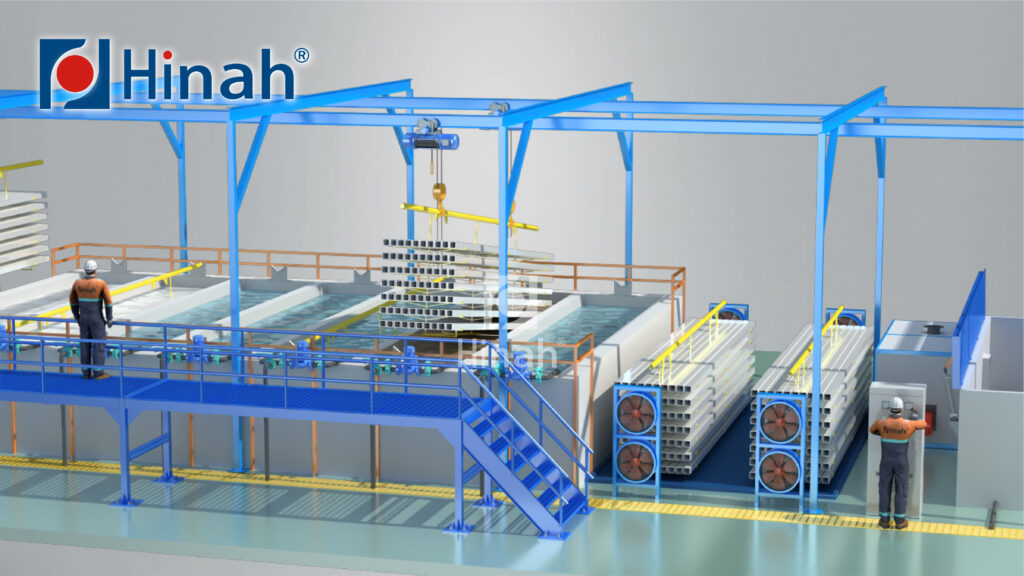
II. Spray Pretreatment Systems: High-Efficiency Surface Preparation
Spray pretreatment is an automated surface cleaning and chemical treatment process integral to industrial powder coating equipment lines. Parts are conveyed through an enclosed stainless steel tunnel where precisely sequenced chemical sprays prepare surfaces for powder adhesion. This method dominates high-volume production due to its speed and consistency.
Operational Workflow
Stage 1: Alkaline Cleaning Spray
Heated alkaline solutions are propelled through nozzles at 15-30 psi pressure. This removes oils, greases, and particulate contaminants in 60-90 seconds. Advanced systems feature multi-stage filtration and chemical recycling, reducing waste by 25-30%.
Stage 2: Rinsing & Surface Activation
High-volume rinse sprays eliminate alkaline residues, preventing cross-contamination. An acidic or conditioner-based activation spray then micro-etches the metal surface. Real-time water quality monitoring maintains impurity levels below 50 ppm, often using reverse osmosis technology.
Stage 3: Phosphate Conversion Coating
Zinc or iron phosphate solutions are atomized via V-jet nozzles to form a microcrystalline layer. This layer enhances corrosion resistance and ensures powder adhesion.
Stage 4: Sealing & Final Rinse
A chrome-free sealer spray locks the phosphate layer, followed by a deionized water rinse to prevent mineral spotting. Parts exit through a hot-air dryer ready for powder application.
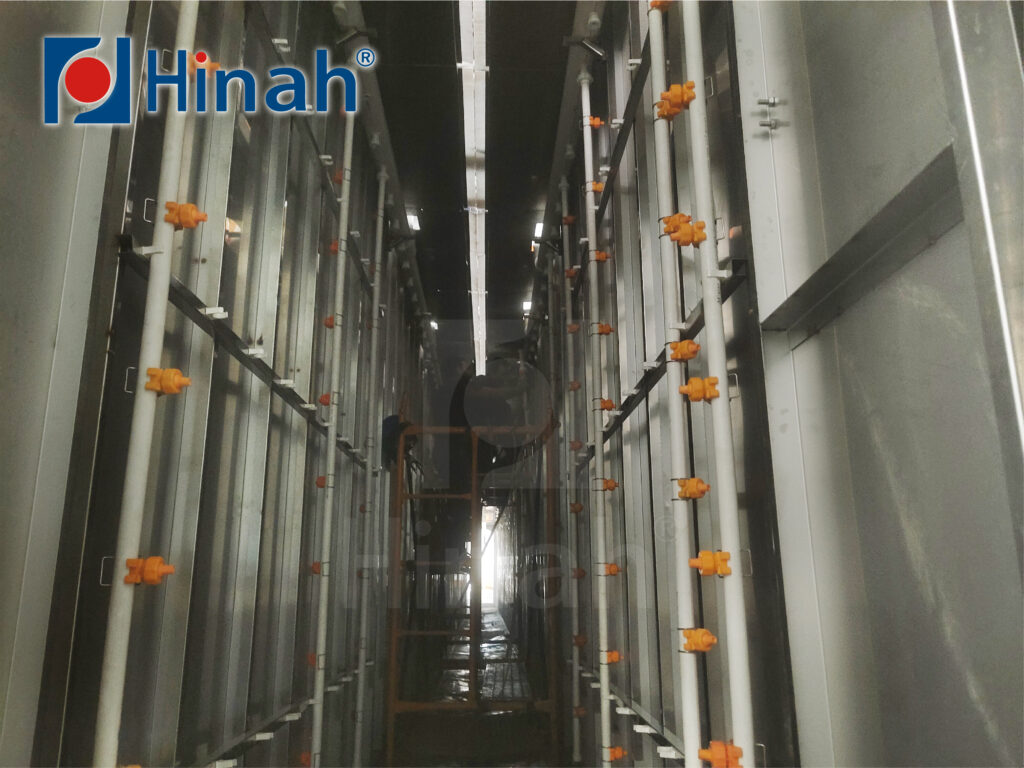
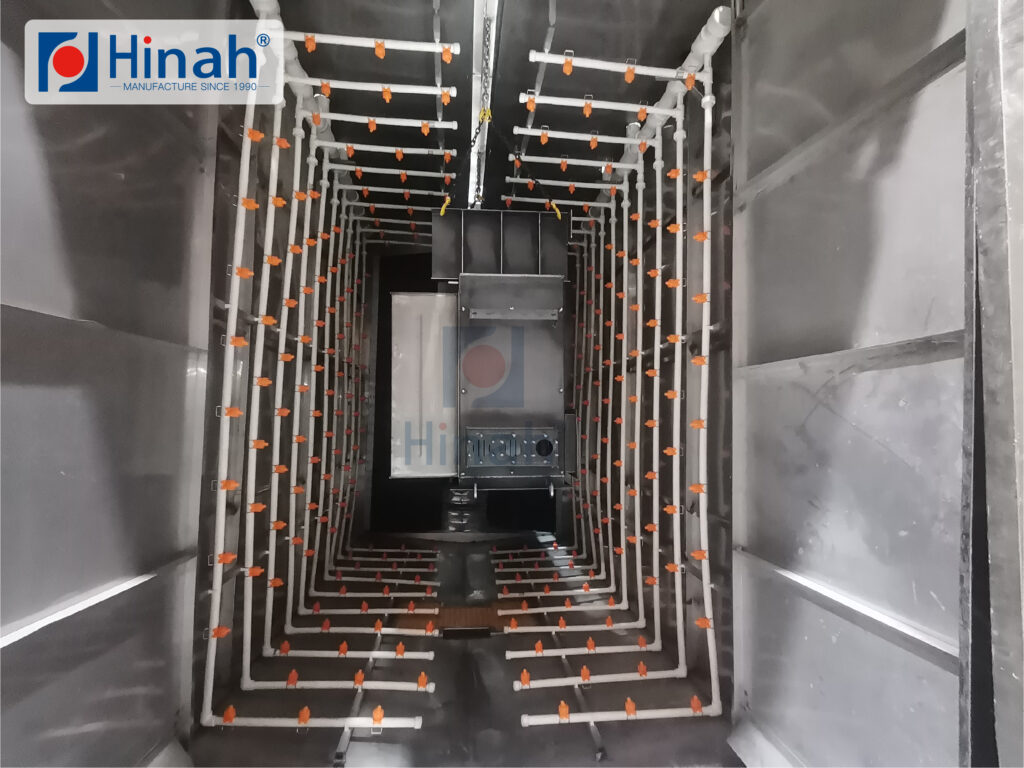
III. Dip-tank Pretreatment Systems: Complete Coverage for Complex Parts
Dip-tank pretreatment submerges components in sequenced chemical baths to achieve thorough surface preparation – the preferred method for intricate or heavily contaminated parts in industrial powder coating equipment. Unlike spray systems, dip-tank ensures complete penetration of cavities, welds, and internal geometries.
Operational Workflow
Stage 1: Alkaline Soak Cleaning
Parts are submerged in heated alkaline solutions for 3-8 minutes. Agitation systems create turbulent flow to dislodge stubborn oils and scale. Extended dwell times allow chemicals to penetrate complex structures impossible for spray systems.
Stage 2: Multi-Tank Rinsing
Components transfer through cascading rinse tanks via overhead hoists. Counter-current flow design maintains water purity:
- Tank 1: Overflow rinse removes gross contaminants
- Tank 2: Agitated immersion with <100 ppm impurities
- Tank 3: Final deionized rinse
Stage 3: Dip-tank Phosphating
Zinc or manganese phosphate baths form microcrystalline layers over 5-15 minutes. Continuous filtration removes sludge while automated titration maintains:
- Total Acid (TA): 18-25 points
- Free Acid (FA): 0.8-1.2 points
- Accelerator levels: 0.8-1.5 mL
Stage 4: Chromium-Free Sealing
A final dip in tricationic sealant closes phosphate pores and enhances corrosion resistance. Parts exit through air knives and IR dryers.

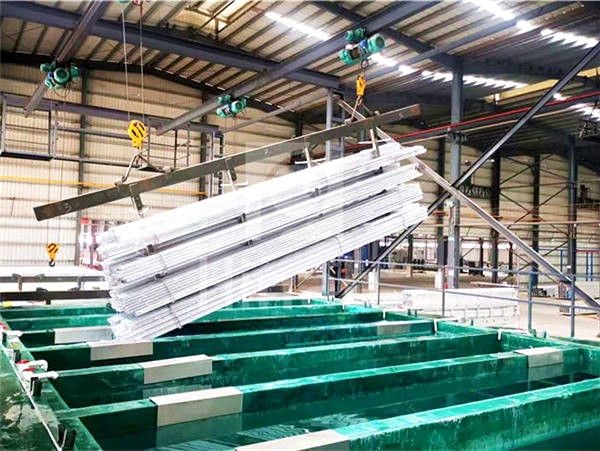
Conclusion: The Strategic Heart of Powder Coating Success
Pretreatment is where every lasting powder-coated finish begins, and the choice between spray anddip-tank systems hinges entirely on your parts’ geometry and production goals. Spray pretreatment excels for simple, flat components—like enclosures or panels—delivering rapid cleaning through targeted high-pressure jets in streamlined tunnels. It’s the go-to for high-volume lines prioritizing efficiency. Dip-tank pretreatment, by contrast, submerges complex or heavily contoured parts—think welded assemblies or structural fabrications—in sequenced chemical baths. This ensures complete coverage in cavities and seams where spray cannot reach.
Selecting the wrong method risks adhesion failures: spray may leave blind spots on intricate parts, while dip-tank could slow throughput for simple items. Let your components guide you: uncomplicated shapes align with spray’s speed, while complex geometries demand dip-tank’s thoroughness. Partner with specialists to audit your workflow, integrate the right pretreatment stage, and build a powder coating equipment line that eliminates defects at the source. Lasting quality isn’t sprayed on—it’s built from the ground up.