Key Advantages of Using an Industrial Powder Coating Machine
For manufacturers facing daily pressures – hitting targets, controlling costs, and ensuring quality – every piece of equipment needs to pull its weight. Powder coating delivers a tough, attractive finish, but the real difference comes down to the machine applying it. Small setups or manual methods often can’t keep up with real-world production demands, leading to bottlenecks and inconsistency.
This article cuts through the noise to highlight the concrete benefits of investing in a dedicated powder coating machine for your industrial operation. We’ll look at how these systems directly tackle common challenges, boosting your output, slashing waste, improving finish reliability, and making your whole coating process smoother and safer – putting real value on your shop floor.
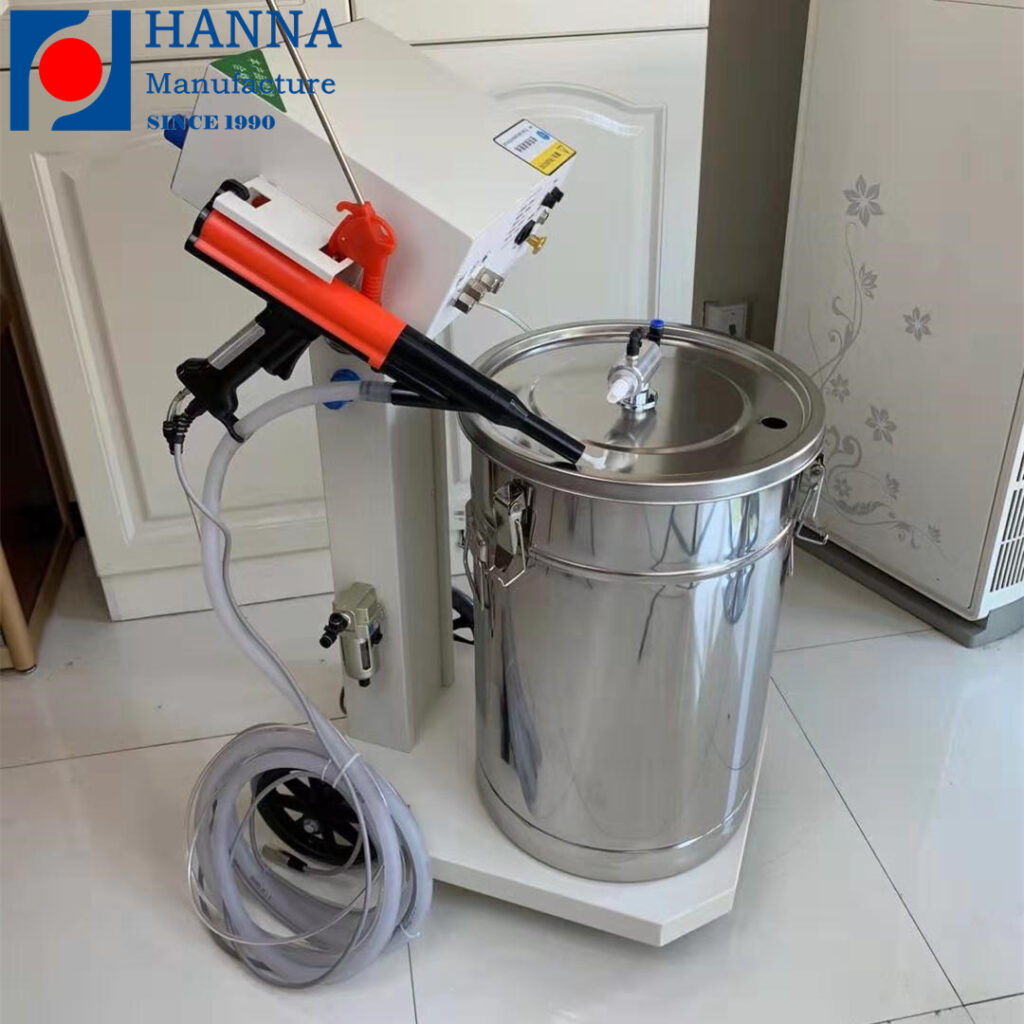
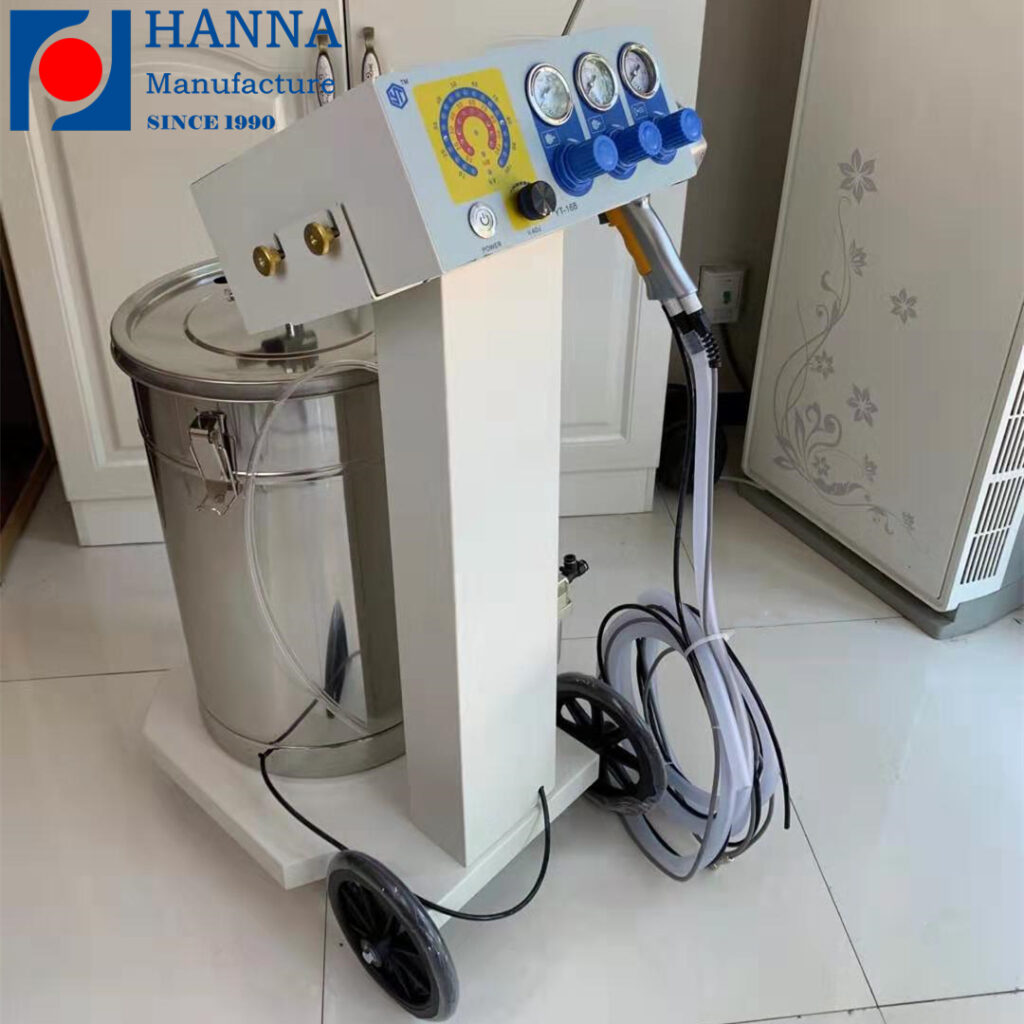
Superior Finish Quality & Consistency: Why Precision Matters
In coating operations, inconsistent finishes aren’t just cosmetic flaws—they’re costly. Rejects, rework, and customer complaints eat into margins. This is where an industrial powder coating machine delivers immediate value: it removes human variables from the equation.
How Your Powder Coating Machine Achieves Unmatched Uniformity
- Automated Control, Not Guesswork:
Programmable settings ensure every part receives identical spray patterns, gun distance, and pressure. No more “light passes” or heavy overlaps from manual spraying.
- Eliminating Common Defects:
Orange peel, thin edges, and drips vanish. Electrostatic application in a controlled booth means powder adheres evenly—even on complex geometries—right out of the oven.
- Exact Film Thickness, Every Time:
Meet specs reliably (e.g., 60–80 μm). Critical for corrosion resistance, electrical insulation, or USDA/FDA compliance. Too thin? Protection fails. Too thick? Wasted material.
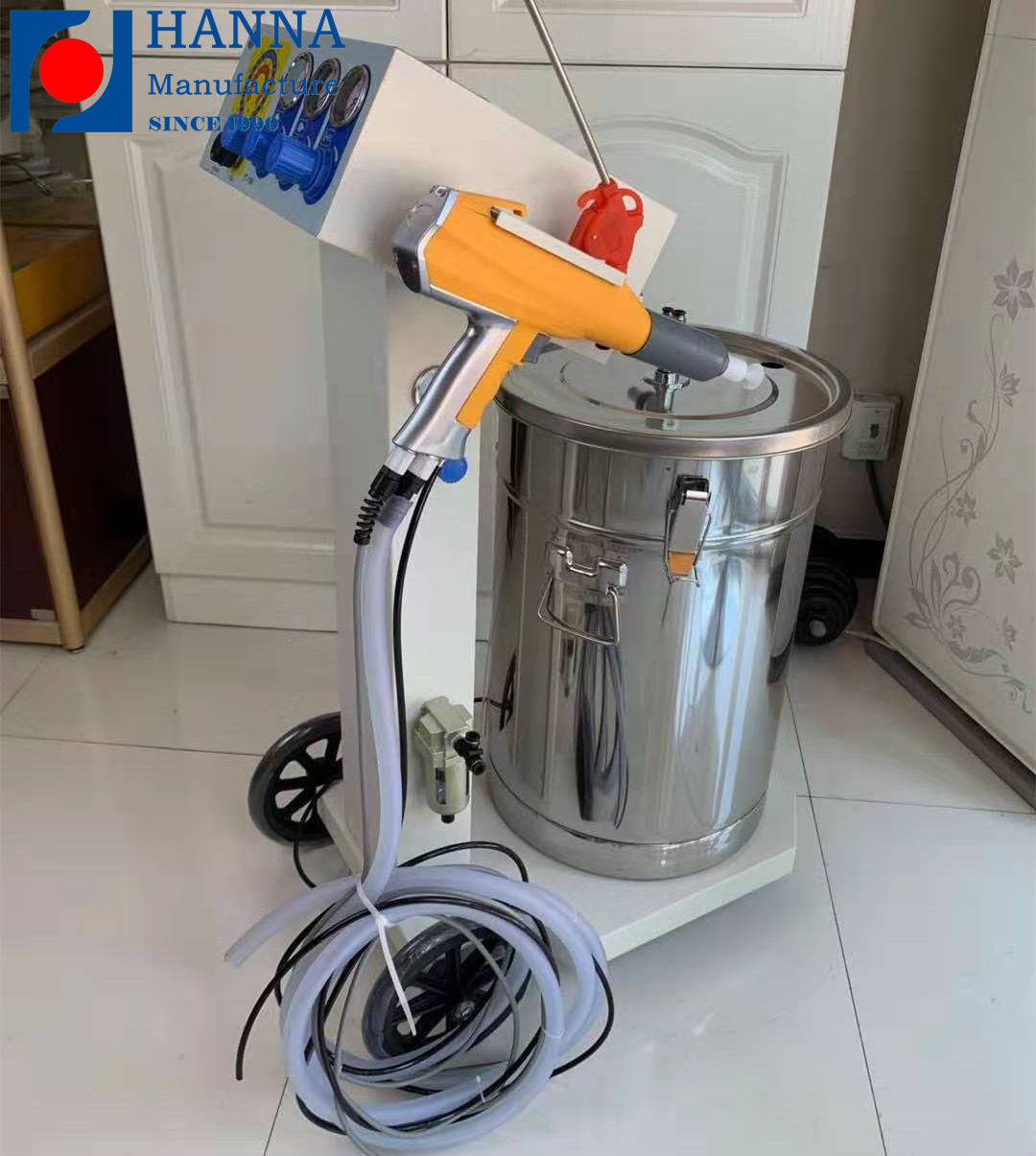
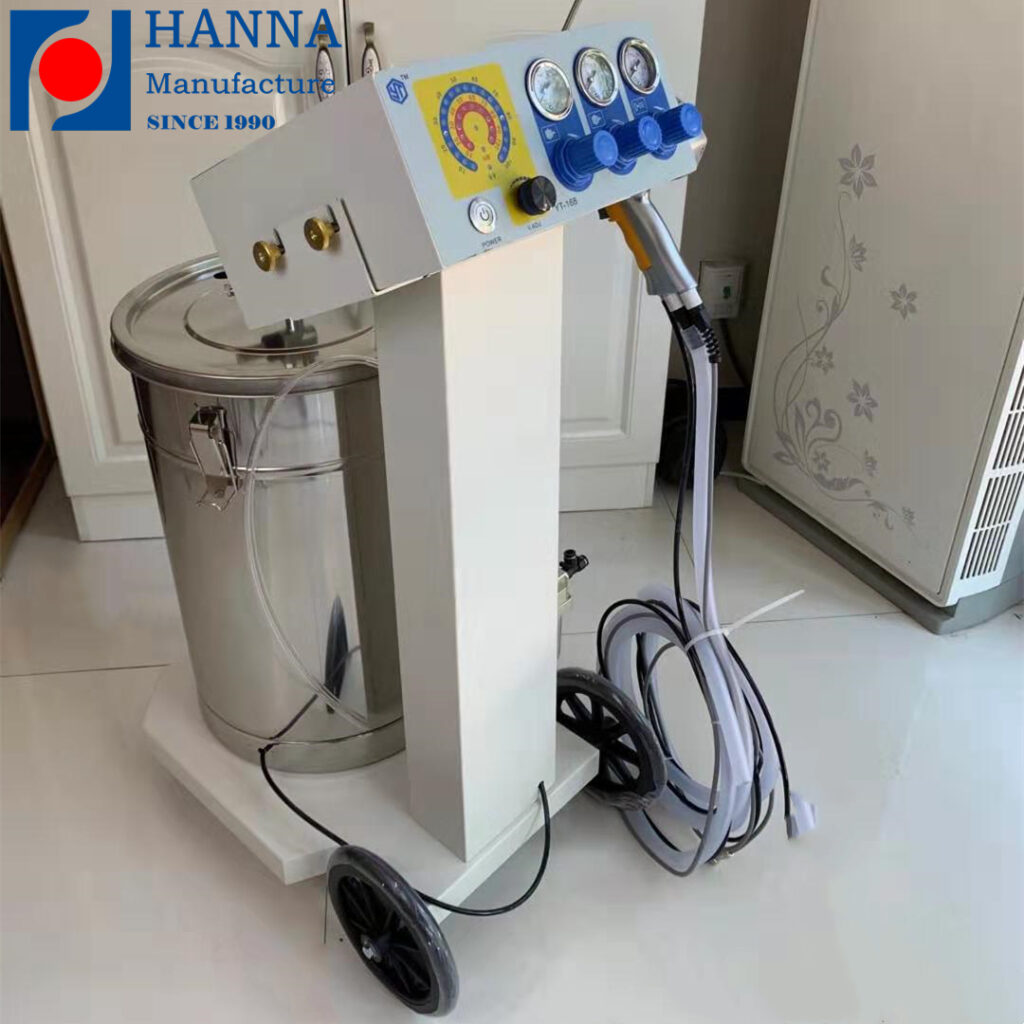
Enhanced Production Efficiency & Throughput
Stop waiting on coating. An industrial powder coating machine slashes cycle times by automating the entire workflow—parts glide continuously through prep, coating, and curing on synchronized conveyors. Forget manual spraying pauses or batch reloading: load large racks once and let the system handle high-volume runs uninterrupted. Digital recipe recall cuts changeover from 30+ minutes to under 10, while reclaim systems capture and reuse overspray instantly, eliminating downtime for booth cleanouts. The result? Triple your throughput, maximize oven utilization, and free operators for value-added tasks.
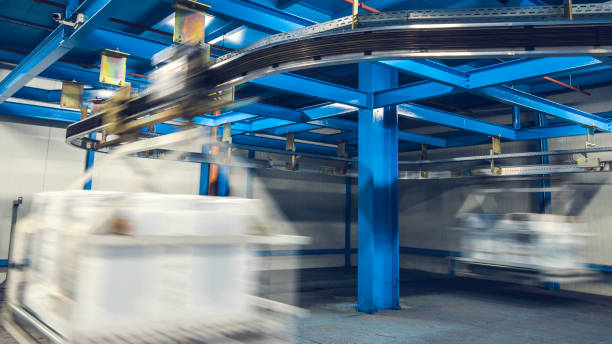
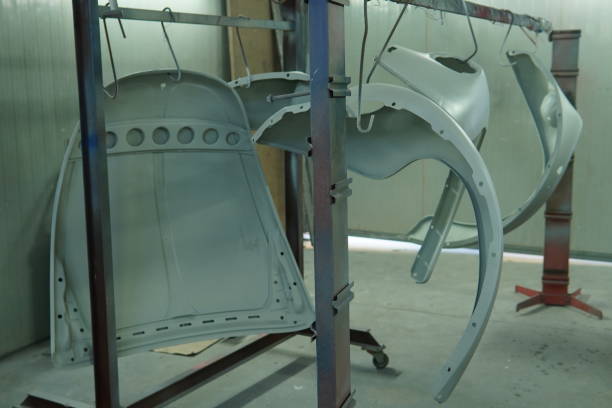
Reduced Material Waste & Operating Costs: Leaner Operations, Stronger Margins
Every speck of oversprayed powder is money lost—and manual spraying wastes far more than most shops realize. An industrial powder coating machine tackles this head-on with intelligent reclaim systems that capture stray powder, clean it, and feed it straight back into production. You’re not just coating parts; you’re maximizing every gram of material. Paired with precision application, this means dramatically less waste per job and fewer bulk powder orders eating into your budget.
But the savings multiply beyond materials. Consistent first-pass quality slashes the hidden drains of rework—no more labor-hours spent stripping defects, no extra oven cycles burning energy on do-overs. You’ll also eliminate costly solvents for cleanup and cut hazardous waste fees entirely.
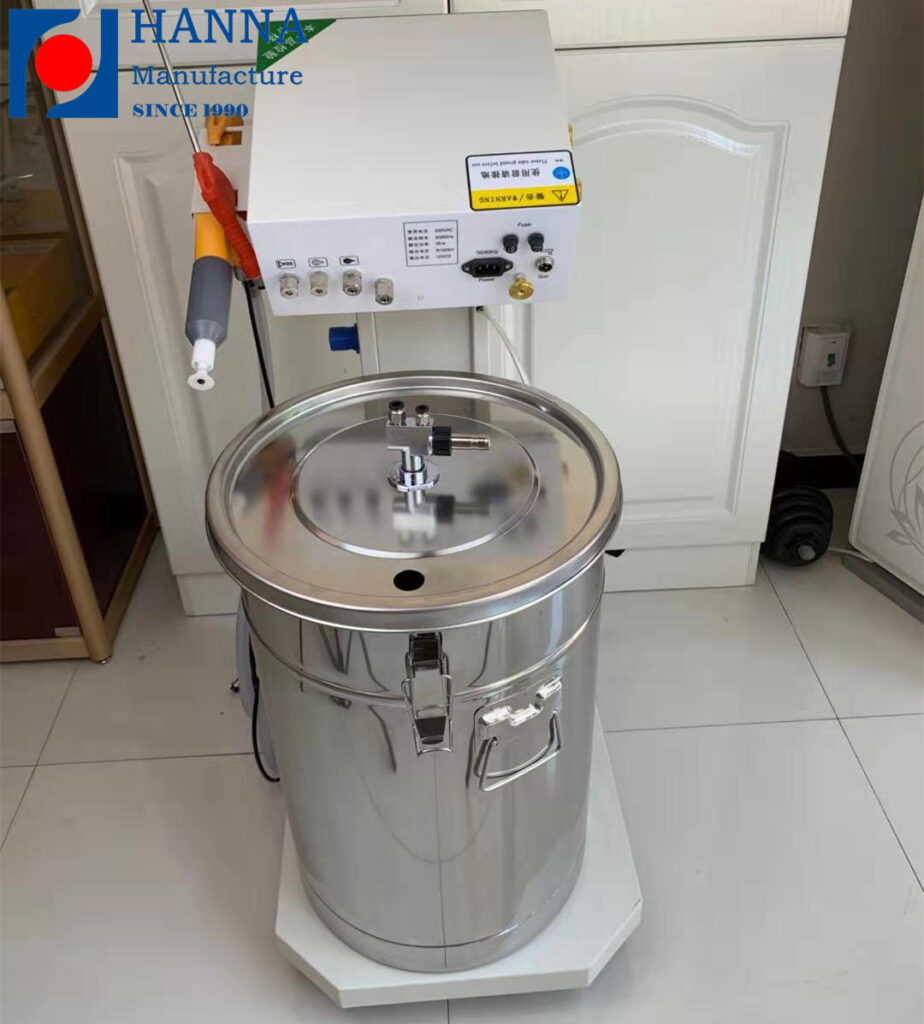
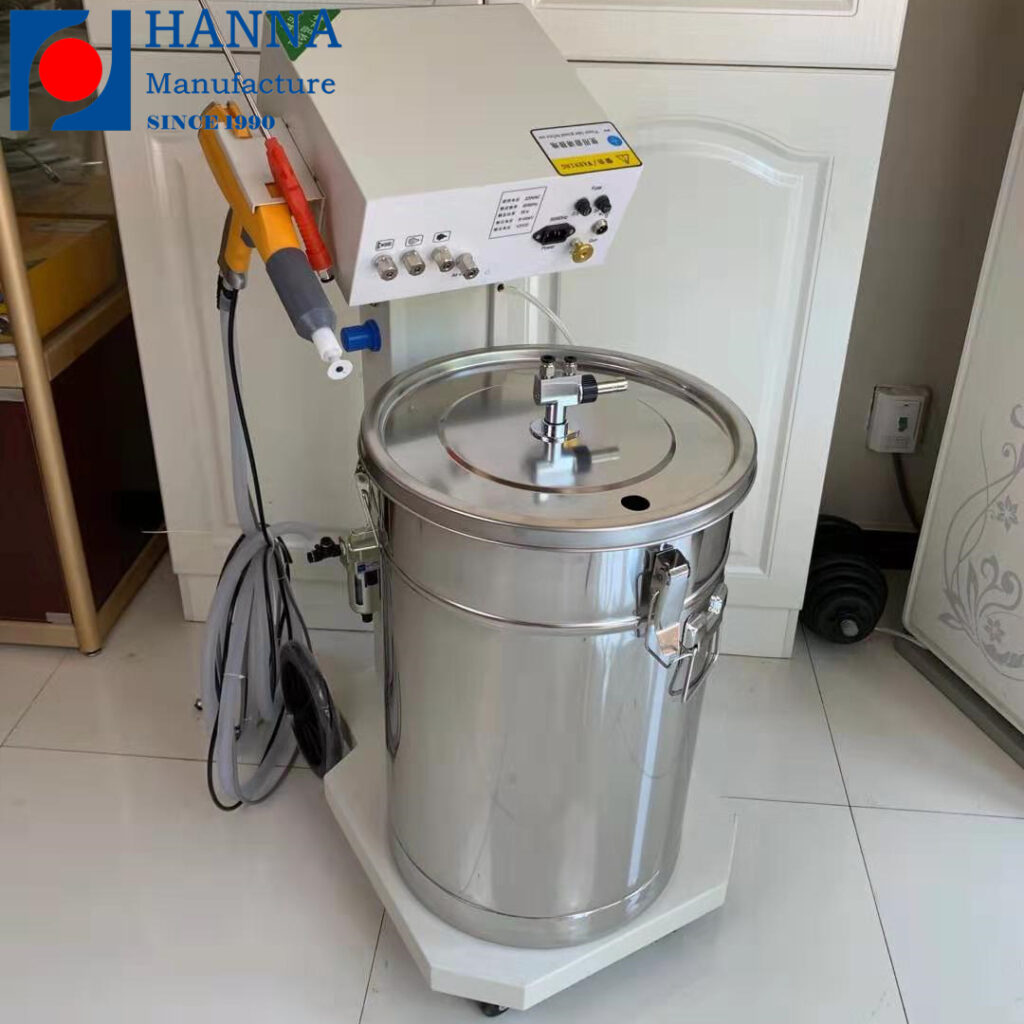
Flexibility for Complex Applications
In real-world manufacturing, no two parts are alike. You might coat delicate medical trays one day and heavy tractor components the next. Manual systems struggle with this variability—but an industrial powder coating machine adapts on the fly. Its programmable controls and modular design handle intricate geometries, mixed materials, and rapid job changes effortlessly.
How Your Powder Coating Machine Masters Complexity
- Conquering Tricky Geometries:
Adjustable voltage/current settings ensure powder wraps evenly around edges, recesses, and thin profiles—no thin spots or Faraday cage effect. Ideal for wire racks, radiators, or textured surfaces.
- Material Versatility Beyond Steel:
From aluminum and magnesium to treated plastics (with primer), your machine maintains finish integrity where manual spraying fails. No more adhesion testing guesswork.
- Instant Switch Between Specialties:
Running antimicrobial powder for food equipment? Swap to heat-resistant ceramic for exhaust parts in minutes. Recipe presets retain flow settings, curing temps, and gun parameters.
- Size-Agnostic Processing:
Modular conveyors and adjustable booths coat everything from M6 bolts to 3-meter panels without retrofitting. Maximize capacity without constant reconfiguration.